Learn the 7 crucial cost escalation factors in construction projects. Discover how material costs, labor shortages, inflation, and unforeseen circumstances can impact your project’s budget. Understand these drivers to better manage your costs. Cost Escalation Factors in Construction:
7 Critical Cost Escalation Factors in Construction You Need to Know
In the dynamic world of construction, cost escalation is a common challenge that can disrupt project budgets and timelines. With the constant changes in economic conditions, material costs, and labor availability, it’s crucial for project managers, contractors, and estimators to understand the factors that contribute to cost escalation. By identifying these factors early on, you can manage your budget more effectively and reduce the risks of unforeseen financial burdens.
In this blog post, we will explore seven key cost escalation factors that can impact construction projects and discuss how to mitigate their effects.
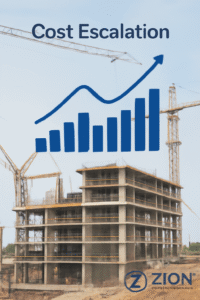
1. Material Costs and Price Volatility
One of the most significant cost escalation factors is the fluctuating prices of construction materials. Materials such as steel, cement, lumber, and concrete often experience price volatility due to supply chain disruptions, changes in demand, and the costs of raw materials. For example, the global pandemic has caused a surge in the price of building materials, which has resulted in cost increases for many construction projects.
How to Manage Material Costs:
-
Establish Early Procurement Plans: Secure materials early in the project phase to lock in prices before they increase.
-
Negotiate Bulk Pricing: Purchase materials in bulk to take advantage of lower rates.
-
Source Locally: Find suppliers closer to the project site to reduce transportation costs and risks of delays.
2. Labor Shortages and Wage Inflation
Labor is another major contributor to construction cost escalation. With a shortage of skilled workers in many regions, wages for skilled labor have increased significantly. The lack of qualified workers can also lead to project delays, causing labor costs to rise. This issue is exacerbated when labor markets are competitive, as contractors may have to offer higher wages to attract qualified workers.
How to Manage Labor Costs:
-
Invest in Training: Provide in-house training programs to develop skilled labor.
-
Plan for Labor Availability: Understand the local labor market and adjust project timelines and budgets accordingly.
-
Outsource Labor: Consider outsourcing tasks that can be performed by less specialized workers to reduce labor costs.
3. Inflation and Economic Conditions
Inflation is an economic factor that drives the cost of materials, wages, and equipment rental prices up. When inflation rates rise, the purchasing power of the budget decreases, making it more expensive to carry out construction work. Construction contracts often include clauses for inflation adjustment, but many projects are still affected by unforeseen economic changes.
How to Manage Inflation Risks:
-
Use Escalation Clauses: Include inflation clauses in contracts to account for rising costs over time.
-
Monitor Economic Indicators: Stay informed about macroeconomic trends that could impact costs.
-
Flexible Budgeting: Set aside a contingency fund to cover unexpected price hikes.
4. Fuel and Energy Prices
The cost of fuel has a direct effect on the price of construction equipment, machinery, and transportation. Fuel price volatility can lead to unexpected increases in the cost of operating machinery or transporting materials to the construction site. For example, spikes in oil prices can have an immediate effect on construction costs.
How to Manage Fuel Price Risks:
-
Choose Energy-Efficient Equipment: Invest in machinery that is energy-efficient to reduce fuel consumption.
-
Negotiate Fuel Prices: Consider locking in fuel prices through long-term contracts to mitigate short-term price fluctuations.
-
Optimize Logistics: Plan material transportation more effectively to minimize fuel usage.
5. Unforeseen Site Conditions
Unforeseen site conditions can significantly affect the budget of a construction project. These conditions include problems like poor soil quality, the discovery of hazardous materials, or the need for unexpected site remediation. When these issues arise, they can cause delays, require additional work, and ultimately increase the overall project cost.
How to Manage Unforeseen Site Conditions:
-
Conduct Thorough Site Surveys: Perform detailed geological and environmental surveys before starting the project to identify potential issues early.
-
Include Contingency Plans: Build contingencies into your budget to account for unexpected challenges.
-
Work with Experienced Contractors: Experienced contractors can help mitigate risks related to unforeseen conditions.
6. Regulatory Changes and Compliance Costs
Changes in building codes, environmental regulations, and other local or national laws can lead to unexpected cost escalations. If new regulations are introduced during the construction phase, the project might need to comply with additional standards, which can add to both the cost and timeline of the project.
How to Manage Regulatory Risks:
-
Stay Updated on Legislation: Keep track of local and national regulations that may affect your project.
-
Consult Legal Experts: Work with legal experts to understand the regulatory environment and minimize compliance costs.
-
Design Flexibility: Ensure that the design of your project allows for adjustments should regulations change.
7. Environmental and Weather Factors
Weather conditions and environmental factors can cause delays, requiring additional resources to be allocated to the project. Severe weather events such as storms, floods, or extreme temperatures can halt construction activities, leading to cost escalations for labor and equipment usage. Additionally, construction activities that impact the environment may require mitigation measures, further adding to the project cost.
How to Manage Environmental and Weather Risks:
-
Use Weather-Resilient Materials: Choose materials that can withstand harsh weather conditions.
-
Monitor Weather Forecasts: Keep track of weather conditions and plan your project schedule to avoid weather-related delays.
-
Build in Buffer Time: Include extra time in your schedule to account for weather disruptions.
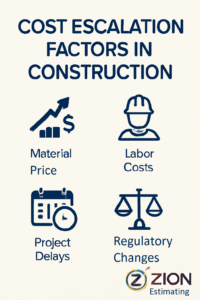
How to Manage Cost Escalation Effectively
While it’s impossible to entirely eliminate cost escalation factors, you can take steps to reduce their impact on your construction project:
-
Accurate Estimating: Use reliable estimating methods, such as parametric or analogous estimating, to create more accurate project budgets.
-
Risk Management: Develop a comprehensive risk management plan to address potential cost escalations.
-
Contract Clauses: Include escalation clauses in contracts to protect against price increases during the project.
-
Regular Monitoring: Continuously monitor the project’s budget and schedule to identify and address cost escalations early.
Conclusion
Cost escalation is a significant challenge in the construction industry. Factors such as material price volatility, labor shortages, inflation, fuel prices, unforeseen site conditions, regulatory changes, and environmental risks can all contribute to increased project costs. By understanding these factors and taking proactive steps to manage them, construction professionals can better control their budgets and minimize financial risks.
Take Action Today:
Stay ahead of cost escalation by implementing these strategies in your next construction project. For more advice on cost estimating and construction management, reach out to Zion Estimating Services Inc. for expert guidance.
Cost Escalation Factors in Construction
Contact Information for Zion Estimating:
- Phone Number:Â 718-427-9941
- Email Address:Â [email protected]
- Website:Â https://zionestimating.com